Post #6- Santa’s workshop (I just wish I had some elves)
Prototypes are almost always a necessary step in the game design process. Once you have an idea, the next step is see if it works. (Spoiler alert, it almost NEVER does the first time around…or second… or third). Depending on the game, a prototype could be a handful of index cards with scribbles on them, stacks of dice (rolled, moved or otherwise manipulated), pawns, meeples or plastic green army men … or a combination of any of these items. Boards can be sketched out on notebook paper, crayon on cereal box pieces or hexes cut from Amazon boxes. and taped together. (A little hint on making hexes, look them up online and print the basic shapes before you cut them. Way easier.) Whatever it takes to get the idea out of your head and on the table in front of players. And the sooner and faster, the better.
Now every game idea has two factors; the “fun” factor (we want more of this) and the “suck” factor (none of this, please). Our job as game designers is to “fail faster”. Let the suck come out in all its glory then rip it out by the roots and let the fun factor blossom and flourish. Sometimes when we prune back everything that doesn’t work, there’s nothing left. Cross that idea off the list and take the next one. Every designer I’ve listened to has a long list of game ideas. If you don’t, you need to start keeping some kind of journal or log and jot down ideas as they come to you. I keep mine on a note in my phone. I literally keep everything on my phone. (I just checked and I am two notes away from 1000 different notes on my phone. They cover everything from grocery lists to story ideas to game ideas and game particulars. But that’s a story for another time.)
As I’ve discussed in other blog posts, making prototypes is a part of the journey of a game designer I enjoy the most. I’ve been making graphic designs for a really long time and although I probably wouldn’t hire myself out as a graphic designer I feel like I do a decent enough job at least for prototyping. I’ve also come up with some pretty cool ways IMNSHO of making the finished product.
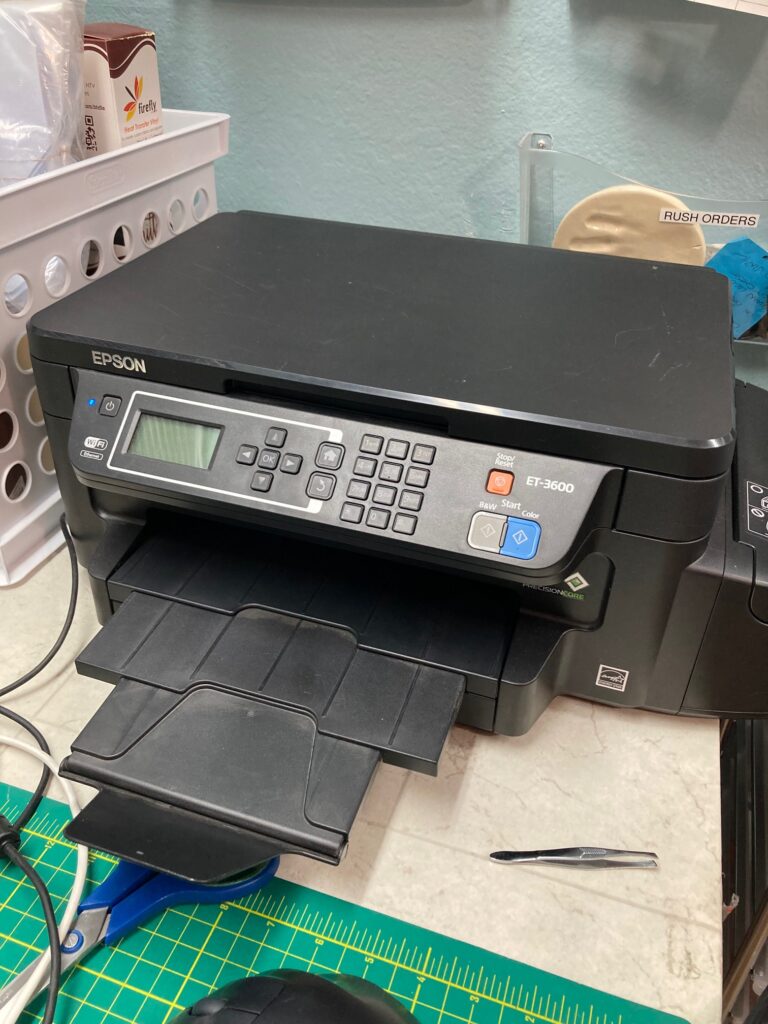
This is my inkjet printer, an Epson ET – 3600 Eco Tank. If you’re printing anything in any kind of volume I highly recommend you pick up something like this. Gone are the days of my spending hundreds and hundreds of dollars on ink cartridges that seem to last a week. I can buy bottles of ink that will refill my printer a couple of times for less than $20 on Amazon. I also have access to a laser printer which is much faster and much of the time produces better results than the inkjet. Either way the process is pretty much the same.
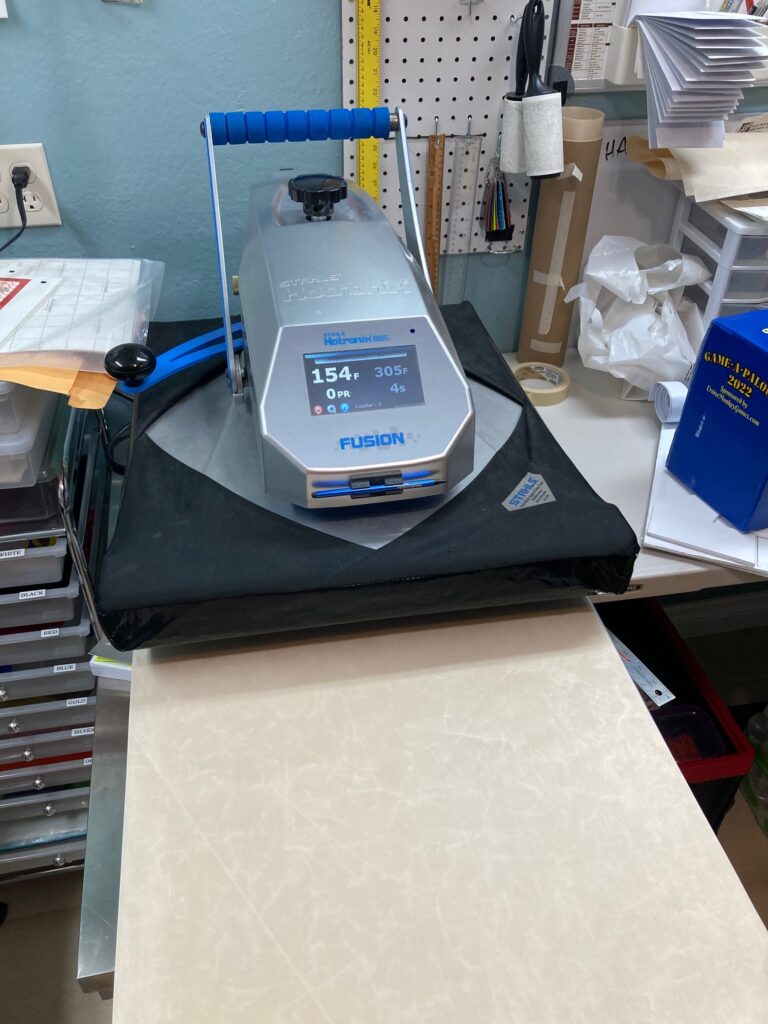
This is my heat press, I bought it to make custom T-shirts. As a matter fact most of the equipment in my hobby room is for that purpose. But after getting into game design I found that it all worked pretty well for making prototypes. The heat press is a Stahl’s Hotronix Fusion, one of the nicest models out there and it has done a great job pressing shirts. It’s also really good at sealing thermal laminating pouches.
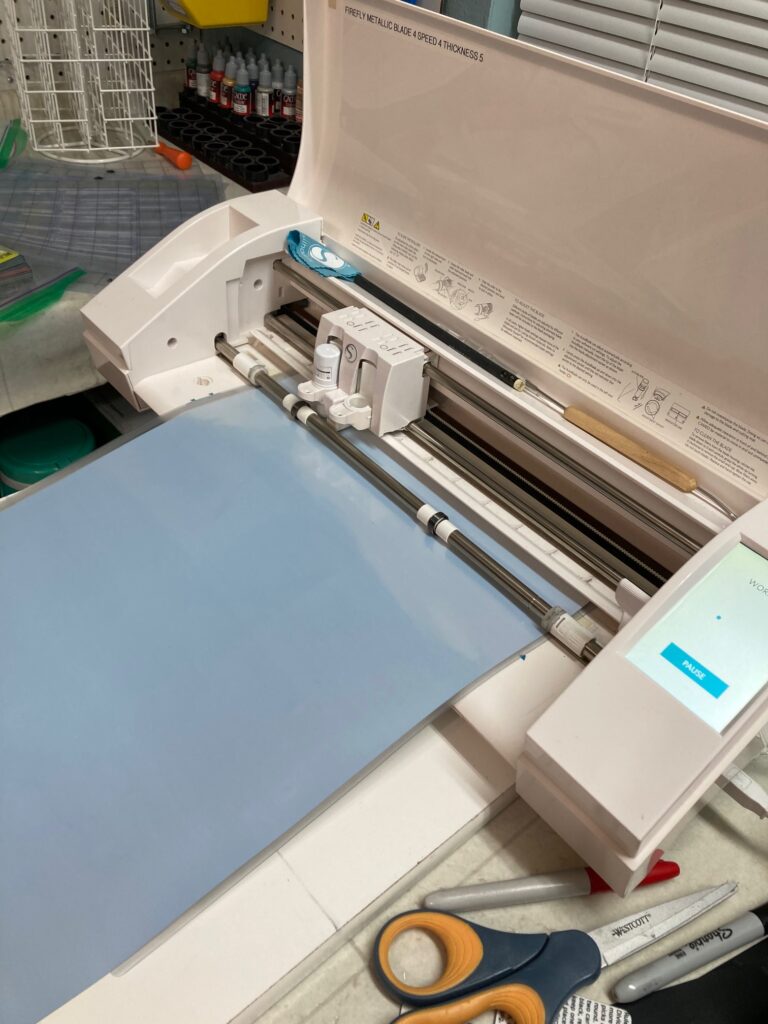
I use the Silhouette Cameo to cut the cards after they’re laminated. Without a doubt that is the one part of this process I am very happy I have a machine to do. I could print cards on just about anything and I could use adhesive pouches to laminate them but cutting them out by hand and trying to make round corners? That’s a lot more difficult. Especially when you consider that One Letter Better has 108 cards in the deck and we’re giving them away every week. (Want a free copy? Check out our homepage for details.) That’s a lot of cutting and clipping.
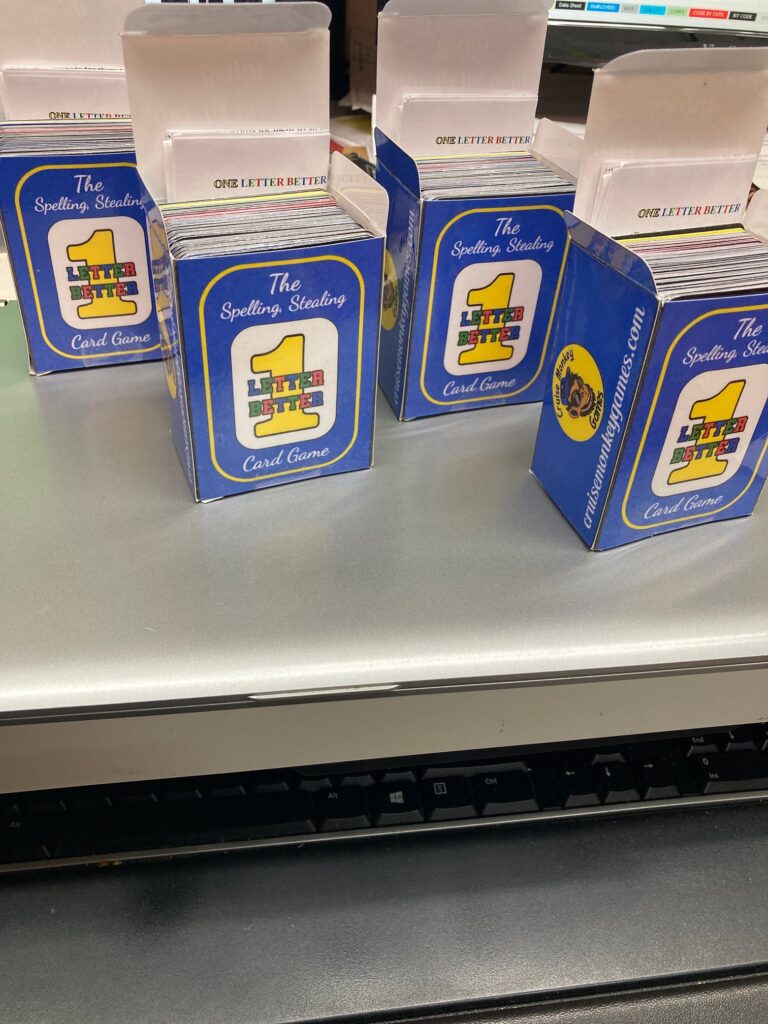
As much fun as it is to see our ideas come to life and become actual playing cards, spending hours and hours printing, laminating and cutting cards does get a little tedious. Especially when you consider that what we’re making are prototypes for people to try out the game and see if they like it. We don’t sell the items that we produce by hand. For one thing, we could never charge enough to make it worth our time. It’s a time-consuming process and there’s just no way to speed it up with the equipment we have. Also, I wouldn’t feel right charging people for the level of quality we have at the moment. When we get to the point of selling our games we will have them professionally produced in a factory where they do that kind of thing every day.

After One Letter Better, we have three more games in the works. The first is 3 Somes, a party game (but not what you’re thinking!) that we’ll be testing tomorrow at Game-A-Palooza. After that we have Biominoes and Hexfinity, Both of which are tile laying games. We print the faces on 8 1/2 x 11 label paper, stick them to foam board and then cut the shapes out. If we want to make them really last we laminate them first. Cesar and I have done some minor play testing with these last two games and they seem solid but we won’t know until we get other people to play them. Until then, we print, laminate and cut ad nauseam. Then play test with the same regularity.
We’re lucky, our games don’t take that long to produce, play test and modify. There are games out there that the designers took five years to get ready for market. That’s a huge investment and something that might never sell. We might get there but if we do, we’re gonna need some elves. Have a great day and make somebody smile.